As the world becomes more and more reliant on aluminum and its alloys, the importance of high-quality welding wire cannot be overstated. Welding is an essential process that allows for the creation of strong, durable, and reliable aluminum-based structures, and the use of the right welding wire plays a critical role in ensuring the integrity of these structures.
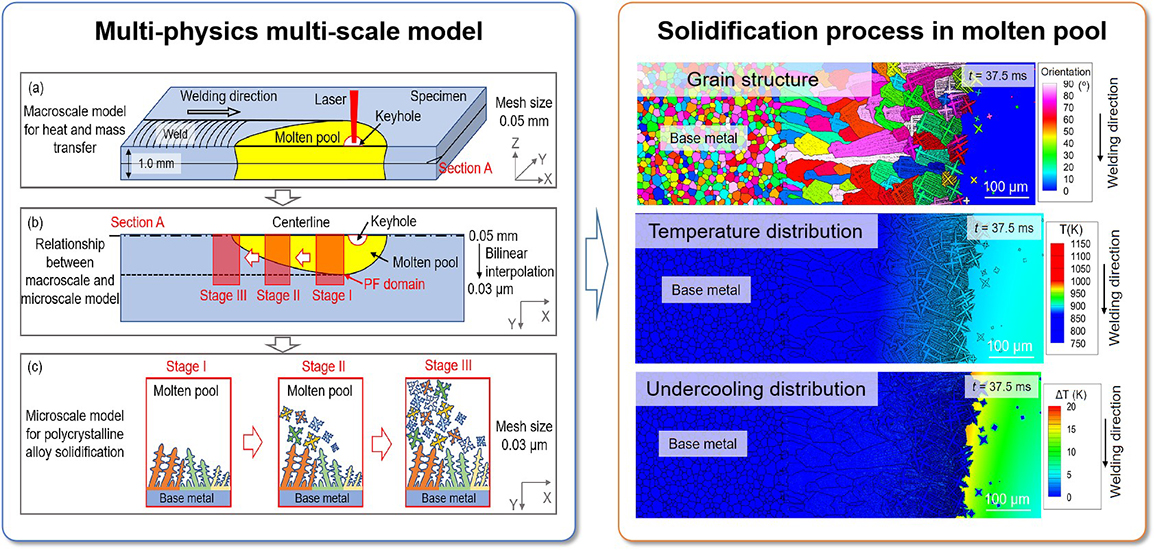
One of the most important aspects of using high-quality aluminum welding wire is the prevention of porosity in the weld deposit. Porosity is caused by the presence of contaminants in the welding wire, which can lead to uneven and weak joints. To avoid porosity, Ceweld aluminum welding wires are shaved twice to remove all contamination under the drawing skin. This ensures that the wire is free of any impurities that could negatively impact the welding process.
In addition, Ceweld applies a special lubricant to the wire surface to improve arc stability and lower friction in the liner and contact tip. This is essential because aluminum wires are prone to becoming dry and generating white dust on the surface. Without the lubricant, the welding wire would be difficult to work with, and the resulting welds could be of poor quality.
The importance of using high-quality welding wire cannot be overstated, and this is especially true in the case of aluminum and its alloys. With its unique properties, aluminum is an incredibly useful material that is used in a wide range of industries, including aerospace, transportation, construction, and electronics. However, aluminum presents several challenges when it comes to welding.
One of the biggest challenges of welding aluminum is its susceptibility to cracking. Aluminum has a high coefficient of thermal expansion, which means that it expands and contracts more than other metals when exposed to heat. This can cause distortion and cracking if the welding process is not done correctly.
Another challenge of aluminum welding is that it requires a significant amount of heat. This is because aluminum has a high thermal conductivity, which means that it can absorb and dissipate heat quickly. If the welding process is not done correctly, the metal can become overheated, which can lead to weakened joints and other issues.
To address these challenges, it is essential to use high-quality welding wire that is specifically designed for aluminum and its alloys. Ceweld aluminum welding wires are designed to provide the highest quality and reliability, ensuring that your welds are strong, durable, and long-lasting.
But high-quality welding wire is just one part of the equation. To achieve the best possible results, it is also important to work with experienced professionals who understand the intricacies of aluminum welding. Jiangsu Xingyong Aluminum Technology Co., Ltd. is one such company that has established itself as a leader in aluminum extrusion, anodizing, processing, and testing. With 18 production lines that include CNC punching, welding, drilling, cutting, bending, shrink, expand, printing, and laser processing, the company is equipped to handle even the most complex aluminum welding projects.
In conclusion, the importance of high-quality welding wire cannot be overstated, especially in the case of aluminum and its alloys. Using the right welding wire can help prevent porosity, improve arc stability, and ensure that your welds are strong, durable, and reliable. At the same time, it is critical to work with experienced professionals who understand the intricacies of aluminum welding and who have access to the right equipment and tools. With the right welding wire and the right expertise, you can achieve exceptional results in even the most challenging aluminum welding projects.