Introduction
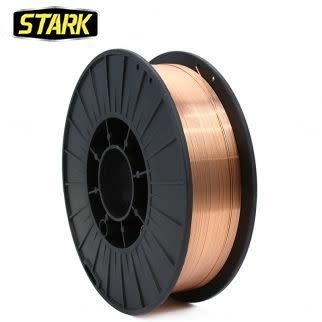
Welding is a vital process in the manufacturing industry. However, the welding process cannot be successful without the use of welding wires. Welding wires are essential in creating a strong bond between pieces of metal. Aluminum welding wires, in particular, are designed to handle the welding of aluminum alloys. ER4043 and ER5356 are two of the most commonly used aluminum welding wires. This article looks at the properties and applications of ER4043 and ER5356 aluminum welding wires, as well as their differences.
ER4043 Aluminum Welding Wire Properties and Applications
ER4043 is a general-purpose aluminum welding wire that is compatible with aluminum alloys 3003, 3004, 5052, 6061, 6063, and casting alloys 43, 355, 356, and 214. The wire is a silicon alloyed aluminum wire that has good fluidity and less sensitivity to hot cracking. It is excellent for use in the welding of cast aluminum parts and is commonly used in the construction of boats, bicycles, and automotive parts.
ER4043 has a tensile strength of 34,000 psi and can weld at temperatures between 1060°F to 1175°F. It produces a smooth and stable arc with a low spatter rate, making it ideal for use in welding applications that require a higher quality finish.
ER5356 Aluminum Welding Wire Characteristics and Uses
ER5356 is a high-strength aluminum welding wire that is mainly used in applications where greater tensile strengths and ductility are required. The wire is compatible with aluminum alloys 5050, 5052, 5083, 5154, 5356, 6061, and 6363. ER5356 has greater resistance to corrosion, especially in saltwater environments and better color matching capabilities after anodizing. It is widely used in the construction of boats, aircraft, and automotive parts.
ER5356 has a tensile strength of 40,000 psi and operates at welding temperatures between 1060°F to 1175°F. The wire produces a smooth arc and is low in spatter, providing a high-quality finish.
Differences Between ER4043 and ER5356
The primary difference between ER4043 and ER5356 is the strength of the weld it produces. ER5356 creates a stronger weld that is more ductile than ER4043. This ability to create a stronger weld makes ER5356 the preferred choice for applications where high-stress levels are expected, such as in the construction of aircraft and boats. ER4043, on the other hand, is ideal for use in general-purpose welding applications where appearance is critical, and strength is not as critical.
Conclusion
In conclusion, ER4043 and ER5356 aluminum welding wires play a critical role in the welding of aluminum alloys. Both welding wires have unique properties that make them ideal for different applications. Knowing the characteristics and uses of these welding wires can help you make the right choice when selecting a welding wire for a specific project. If you need to create a strong weld with greater ductility, ER5356 would be the best choice. However, if you need a pristine finish and appearance is essential, ER4043 would be the ideal option.